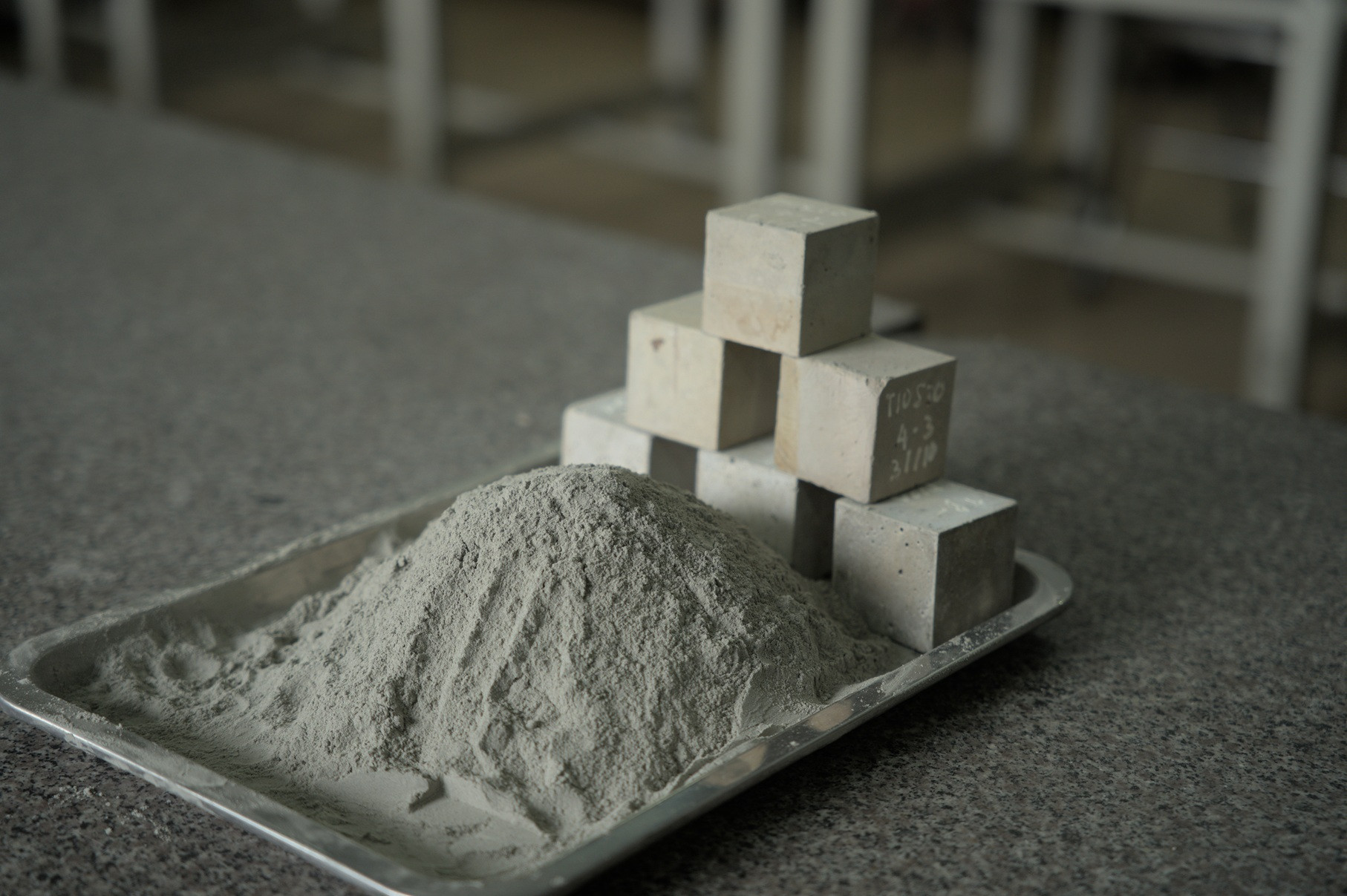
Outshining hundreds of entries, the team of three final-year Materials Engineering students, Dam Duc Son, Nguyen Quang Minh and Doan Dinh Huy, clinched the top spot.
Team leader Dam Duc Son explained that, because of recent complex fire incidents and rising industrial waste, the group devised a solution to address these pressing issues.
The project uses Cenospheres (a substitute for sand) and fly ash from coal-fired power plants to create fire-resistant, heat-insulating mortar. This specialized mortar is sprayed on steel components (basic parts of reinforced concrete or steel structures) in warehouses and industrial buildings.
It helps to increase heat resistance time, thus enhancing structural strength, allowing more time for firefighting or evacuation, and reducing fire-related damage.
“We learned that Cenospheres is an inorganic, non-flammable component in fly ash from power plants. We chose Cenospheres for their lightweight, hollow microstructure, ideal for insulation. We believed that their structure would enhance the mortar’s fire and heat resistance, and after multiple tests, we perfected the product,” Son said.
The mortar created by Son’s team has Cenospheres (replacing sand), fly ash, cement, reinforcing fibers, additives, and water. The mixing ratios are a trade secret that creates special characteristics for products.
Experiments have proved that the mortar outperforms conventional sand-based or other-material mortars in heat resistance.
“When exposed to 300°C flames for five minutes, we found that the temperature of the side touching flame was 300oC, but the temperature of the back side was nearly unchanged at 30-30.5°C,” he said.
“Standard sand-based mortar (using sand and following the standard mixing ratio) saw the temperature of the back side surface rise from 34°C to 85°C. This proves the product’s superior insulation,” he explained.
The other big advantage of the mortar is that it is 20 percent cheaper than other fire-resistant, heat-insulating mortars available on the market, which are often expensive and less accessible to businesses.
It took the team 1.5 years to turn their idea into reality. The biggest challenge was searching for information, as studies on Cenospheres’ mechanical properties in Vietnam were scarce.
“We needed information to calculate the right mix ratio. With the professor’s guidance, we made significant progress to refine the product,” Son recalled.
In addition to experiments in a lab, the team also tested the mortar at two external Hanoi sites, evaluating adhesion, resistance to cracking, and durability, with excellent results.
The students believe that there is currently no unit researching and selling products from this material in Vietnam. “Cenospheres is a fairly new material. It is a waste and can be found in Vietnam, so the cost will not be high,” Son said.
Thanh Hung